Braking story: The history and evolution of car brakes

Mail This Article
Brakes, which are the most fundamental automotive safety technology, have evolved from blocks of wood to precision-engineered systems today.
The earliest form of braking technology can be seen in bullock carts. A wooden block hangs from a rope. The other end of the rope could be tied somewhere in the front. When the driver presses his foot on the rope, the log grinds against the wheels, gradually pulling the cart to a halt. This was the brake system in earlier periods. Wooden blocks and a lever were used by the driver to apply the brake on vehicles with horse-drawn carts with steel-rimmed wheels and early cars. The brake works by converting kinetic energy into heat by friction.
Cable brake
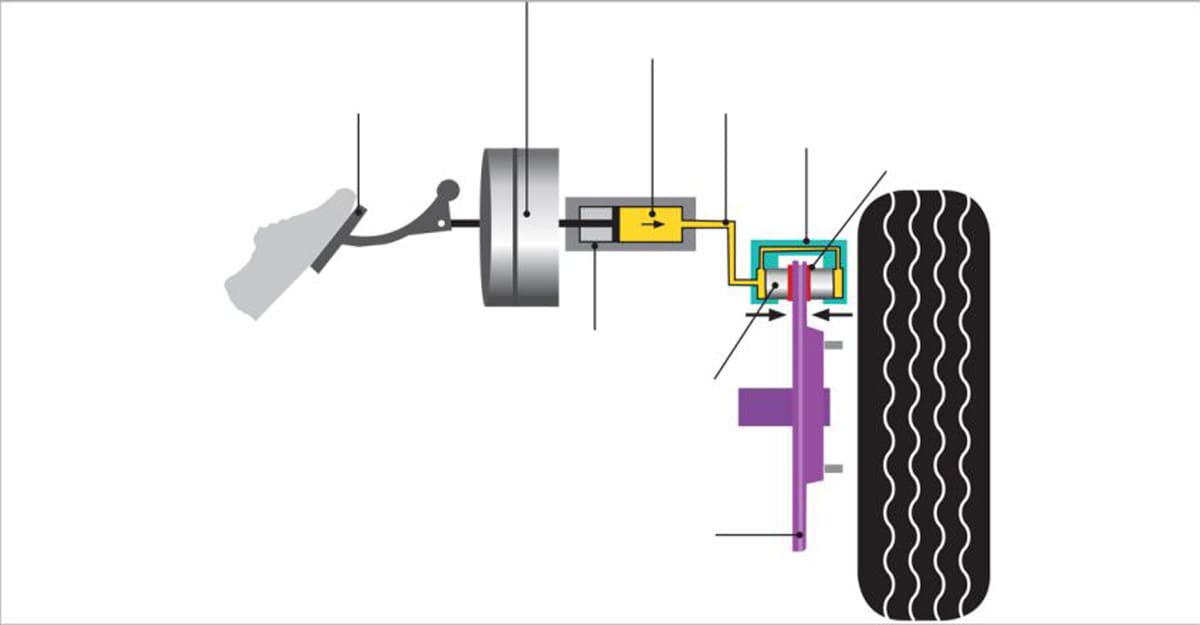
When rubber tyres were introduced by the late 1890s, the steel-rimmed wheels became obsolete and together with it the wooden block brakes. It became useless because the wood grounded the rubber down. Instead, cable-wrapped drum anchored to the vehicles’ chassis to stop momentum was introduced. This idea of Gottlieb Daimler was put to use by Wilhelm Maybach in a Mercedes in 1901.
There were drawbacks with such brakes, including the cables getting unwrapped and giving way while climbing a hill, slipping due to moisture and getting jammed due to dust. In 1902, Louis Renault introduced a new brake system by addressing these issues.
The system contains two brake shoes, one that moves in the drum's direction of rotation and the other that moves against it and is mounted on the rear axle. The brakes are deployed by using brake shoe levers and cables to create friction against a drum connected to the rotating wheel. Modified versions of these drum brakes were used in the decades that followed. Drum brakes are still seen on the rear axle of many new cars.
Hydraulic brakes
The next big step was the shift from mechanical to hydraulic controls. In 1918, Malcolm Loughead put forward a concept of using fluids to transfer force to the brake shoe when a pedal was pressed. Initial response from vehicle manufacturers to the new system was cold. The reason: Operating under high temperatures and high pressure, the fluid could leak. The introduction of better washers and rubber cup seals addressed these issues and hydraulic brakes became widely popular. From only rear wheels, brakes were then fitted into all four wheels, which brought about a sea change in braking that used to be a stroke of luck in high speeds till then. It was Duesenberg that first introduced a model in 1915 that was fitted with brakes on all four wheels.
Power brake
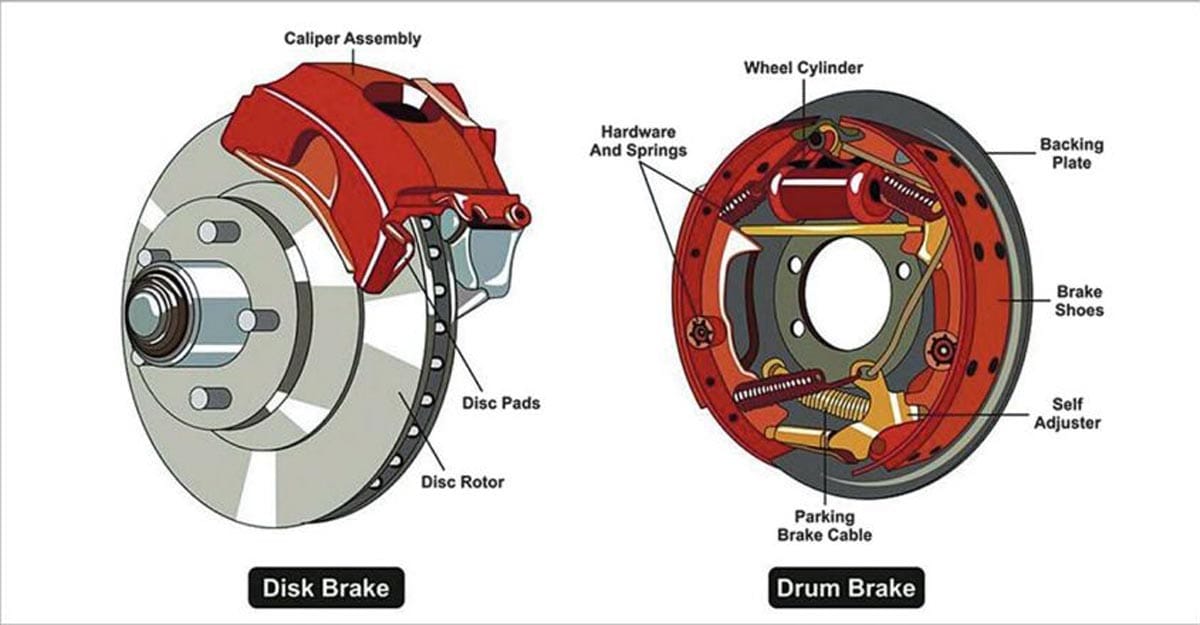
The power brake was the next advancement in the field. Power brakes use a vacuum pump, powered by the intake manifold, to give the driver a power boost and make it easier to apply the brakes. A vacuum-assisted brake boosters is its key component. A master cylinder that is directly controlled by the brake pedal and wheel cylinders that transfer the brake pressure generated in the master cylinder to the drum brake shoes are the other key components.
The vacuum booster of the power brake will be attached to the master cylinder. The vacuum pressure needed for its functioning is provided directly from either the inlet manifold or the pump that is fitted to the alternator. The vacuum power brake first made its appearance in Pierce-Arrow’s 1928 car.
Disc brake
Disc brakes took shape along with drum brakes. In 1898, an electric car made its debut in the US with front-wheel disc brakes. Here, instead of drums, a brake disc (rotor) is fitted to the wheel. Disc brakes use calipers to squeeze a pair of pads against a moving/rotating disc. Disc brakes are designed like common bicycle brakes; instead of the cable in bicycle hydraulic controls are used here. Even though Lanchester company of England used disc bakes in its cars in 1902, it did not click then. Fifty years later, an Austin Healey 100S that hit the road in 1953 had disc brakes for the first time.
Birth of ABS
When the effectiveness of braking systems improved, there arose another issue. In sudden braking, the wheels get locked up, resulting in tyres losing grip and skidding. If the road is wet, or if there is presence of sand or gravel on the road, the problem gets aggravated. To tackle this, the ABS or the anti-lock braking system was developed.
Anti-lock brakes were first introduced by French automobile and aircraft pioneer Gabriel Voisin in 1929 to prevent skidding of airplanes. This was a fully mechanical system. In 1928, Karl Waessel and 1936 Robert Bosch got patent for similar systems. In 1960s, Mario Palazzetti of Fiat Research Centre designed the modern anti-lock braking system that is now standard in all motor vehicles. The patent of this system was later sold to Bosch.
The ABS consists of speed sensors on all four wheels, valves with electrical control and an electronic control unit. ABS uses speed sensors on both wheels to accurately determine wheel speed as well as sensors to determine when a wheel is about to lock. It uses the valves of the wheel cylinder to reduce hydraulic pressure to prevent the wheels from locking during hard braking and retain the grip and control of the tyres.
Another system that works along with the ABS is the electronic brake force distribution (EBD). In fact, EBD is an extension of ABS, making sure that each wheel gets the right amount of braking force. Another system that works along ABS is the brake assist. Brake assist simply allows the ABS system to stop the car even more effectively. A sensor attached to the brake pedal triggers the brake assist system to detect when the driver is attempting to stop in emergency and applies full braking pressure until the car comes to a complete halt.
Ancillary components
Along with the development of braking systems, the design and production of their components too saw big changes. Early brake shoes were made of wood and leather. Later, asbestos came to be used. Though considered the best material to build all sorts of brake pads and shoes, asbestos was discontinued when it came to be known that it causes cancer. Instead of asbestos, brake shoes and pads were made using synthetic materials and metal powder as friction material. Ceramic brake pads that use clay particles and metal fibres are the latest in brake technology. Brake cylinder that was earlier made with iron is now made of aluminium. Developments happened in case of brake fluid too. Composed of several chemical compounds, modern brake fluids offer excellent braking efficiency for long.
Regenerative braking
In conventional brakes, most of the energy of the moving vehicle is lost in the form of heat. Regenerative braking is aimed at conserving energy lost during conventional braking to some extent. With the advent of electric vehicles, another avenue to reduce loss of energy has opened since the motor that helps mobility can also generate power like a generator. In Formula 1 racing cars, kinetic energy recovery system is used for recovering the moving vehicle's kinetic energy under braking. The recovered energy is stored in a flywheel for later use under acceleration.