ISRO fixes snag in Chandrayaan-2 rocket, new launch date shortly
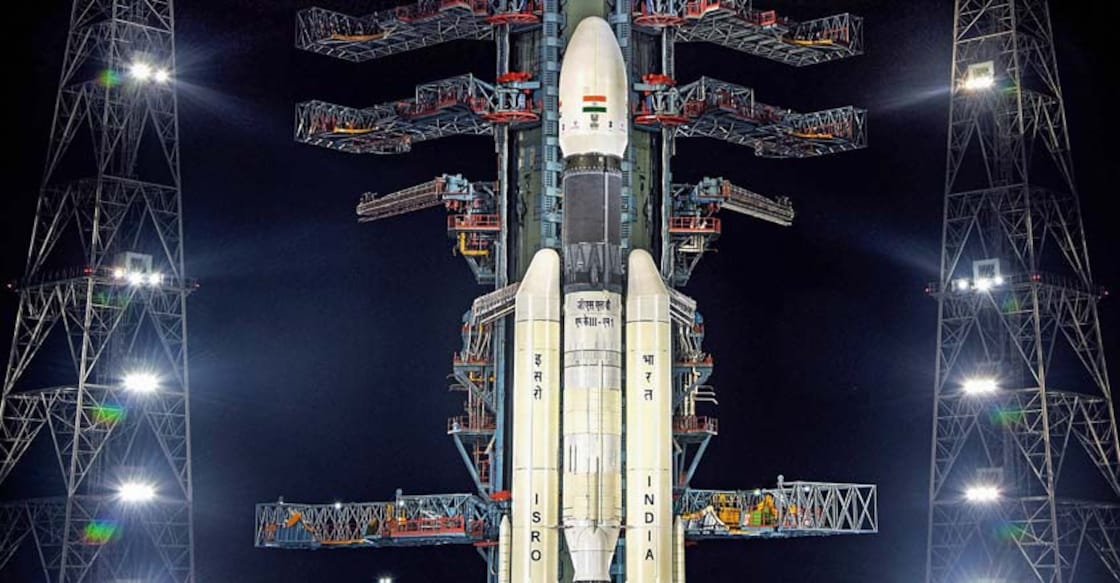
Mail This Article
Chennai: Renewed efforts to ready India's second lunar mission Chandrayaan-2 are on after the first scheduled launch had to be cancelled by the Indian Space Research Organisation (ISRO) at the eleventh hour early on Monday owing to a glitch attributed to the helium tank in the GSLV-Mark III rocket. Latest reports say this issue has been rectified and the space agency is eyeing another bid at launching the lunar craft probably in a few days. The new date of the launch could be announced in a day or two.
It is said non-building of sufficient pressure in the helium tanks of the GSLV-Mark III rocket forced the cancellation of the launch on Monday.
The ISRO has decided to go ahead with the launch at the next best available date even if conditions are not totally perfect.
The rocket Geosynchronous Satellite Launch Vehicle-Mark III (GSLV-Mk III) was supposed to lift off at 2:51am on Monday, July 15, with India's second moon mission spacecraft Chandrayaan-2. If the launch had taken place according to plan, the lander from Chandrayaan would have landed on the moon's surface after 54 days, on September 6.
The ISRO is currently, trying to ensure that the rocket reaches the moon on the same date by adjusting the speed and orbiting path of the rocket. The rocket will take at least 22 days to circle Earth's orbit and move on the Moon's orbit. The agency is trying to shorten the next 28 day duration taken by the spacecraft to reach the Moon's surface.
Sources reveal that the ISRO scientists were able to fix the issue without dismantling the rocket or shedding the fuel.
According to the retired officials of ISRO there should be proper pressure in the liquid fuel tanks so that there is continuous flow of fuel to the combustion chamber.
"While the fuel is fed into the combustion chamber from the bottom, helium gas is filled from the top. It seems sufficient pressure was not being built up and hence the launch was called off," a retired ISRO official informed.
According to him, the flow of fuel to the combustion chamber should be uniform for the rocket to fly.
In 2006, the GSLV-F02 (different variant of GSLV) went out of control less than a minute after lift-off and had to be destroyed in air after it started breaking up.
The reason for the failure, an expert committee in its failure analysis report said, was that a propellant regulator in one of the four strap-on liquid motors had much higher discharge coefficient in its closed condition.
"The reason for this could be an inadvertent error in manufacturing, which escaped the subsequent inspection, and acceptance test procedures. This regulator has functioned satisfactorily in all the previous 50 engines manufactured and tested so far," the report said.
"The primary cause for the failure was the sudden loss of thrust in one out of the four liquid propellant strap-on stages (S4) immediately after lift-off at 0.2 sec. With only three strap-on stages working, there was significant reduction in the control capability," the report said.
"However the vehicle attitude could be controlled till about 50 sec. At the same time the vehicle reached the transonic regime of flight and the vehicle attitude errors built up to large values, resulting in aerodynamic loads exceeding the design limits thus leading to break up of the vehicle," the report added.
According to that report, the thrust of the liquid engines used in the strap-on stages is precisely controlled by a set of regulators.
"Detailed analyses have indicated that in S4 engine the thrust control was not effective. Instead of stabilizing at 5.85 MPa (Mega Pascal) chamber pressure, it reached 7.11 MPa at 2.8 sec. This was much beyond the design limits and the engine failed at 0.2 sec after lift-off, that is 5 sec after its ignition," the report said.
"The larger flow of propellant led to higher operating pressure in the gas generator (4.7 MPa against design specification of 3.6 MPa). Due to this higher operating pressure of the gas generator, the water flow rate into it got reduced. The combined effect of larger flow of propellants and reduced flow of water led to a very high gas temperature of 1,823 K against design specification of 900 K and pressure of 4.7 MPa against the design specification of 3.6 MPa.
"The very high operating pressure and temperature resulted in the structural failure of the gas generator. The consequent abrupt stopping of the turbo pumps that feed propellants at very high pressures to the engines led to loss of thrust of S4 engine.
"The water calibration tests conducted simulating the malfunction of the propellant regulator hardware could closely reproduce the flight phenomenon thereby confirming the larger flow area," the report said.
At that time ISRO ruled out any sabotage theories and said the quality checks and inspections has been strengthened.
Incidentally, even the very first flight of GSLV slated for March 28, 2001, was automatically aborted seconds before the lift-off.
That launch was aborted with the automatic shutdown of the main engine just a second before the lift off.
That too after the four liquid propulsion strap-on boosters started burning.
The automatic shut off system was activated when it sensed that one of the strap-on boosters did not develop the required thrust. The vehicle was immediately disarmed.
The rocket was later flown on January 18, 2001, carrying GSAT-1 satellite.
(With inputs from IANS)